Many supply chain professionals have a mountain of responsibilities and may actually overlook a vital aspect of logistics: the reverse supply chain. However, understanding the real truths behind the question, What is reverse logistics? can be confusing at best. Meanwhile, reverse logistics continues to grow to the top priority list of many companies as e-commerce volumes spike, particularly in aftermarket industries, despite becoming a more difficult process. Understanding the growth of reverse logistics, Globe Newswire states, “The global reverse logistics market is analyzed across several regions such as North America, Europe, Asia-Pacific, and LAMEA. The market across Asia-Pacific contributed the largest share in 2020, holding more than two-fifths of the market. Moreover, the region is estimated to manifest the highest CAGR of 5.1% from 2020 to 2028.” Some companies can combine forward and reverse logistics in one solution across a range of unique services, including the debris removal process, installation and setup of new appliances, and more.
What Is Reverse Logistics?
Reverse logistics includes the management and recycling, reclamation, or repurposing of goods or even returning equipment from leasing businesses. Reverse logistics causes the resource to go a step back in the supply chain. For instance, goods flow in reverse from the customer to the distributor to the manufacturer. This process would also apply to reshipping produce and perishable goods or food and beverage freight to prevent damage or spoilage during the transportation process. Ultimately, reverse logistics can reroute waste to avoid spoilage and reduce total transportation costs.
Why Reverse Logistics Is Important
The answer to the question, What is reverse logistics? naturally begs other questions, such as why is it important and how is reverse logistics an essential part of any supply chain? Further, its complexity opens the door to massive risks. However, a proper understanding of the concept will help a company realize several unique benefits, including the following.
Valuable Product Data
One of the most beneficial advantages that reverse logistics provides is an increase in traceability and quality controls through valuable product data. This organization of data helps shippers make vital corrections needed to avoid issues with returning products and prevent adverse customer experiences. Reverse logistics systems and processes with well-thought-out strategies have the ability to easily collect data with technology and transparency. This data can help shippers understand return rates through fact-based issues, including common product defaults and lifespans.
Loss Reduction and Additional Revenue
To decrease product spoilage and waste, as well as avoid added losses in revenue, proper and streamlined management of goods in the reverse chain must travel up through the supply chain based on clear workflows and processes. An example would be tailored return policies and error-free returns that include online returns merchandise authorization, tracking of the return, and analyzing why it’s necessary.
Cost Reduction
Having an efficient reverse logistics process can reduce costs and allow companies to analyze and track product defects and returns’ rationale more accurately. Streamlined reverse logistics processes allow for savings in different areas, including:
- Storage costs
- Return shipping costs.
- Lower labor costs
- Fewer fraudulent returns
Better Brand Image
Reverse logistics processes allow for increased efficiency and heightened levels of service, which reduce negative publicity directed toward the company. Brands that offer recycling for end-of-life goods also enjoy recognition due to efficiency and sustainable practices. Apple has an example of this with their iPhone trade-in opportunity for its customers. Apple will gain the reputation of striving to save customers money by reclaiming its outdated products’ raw materials, and customers realize the opportunity to save money and receive the newest phone with a lower environmental impact.
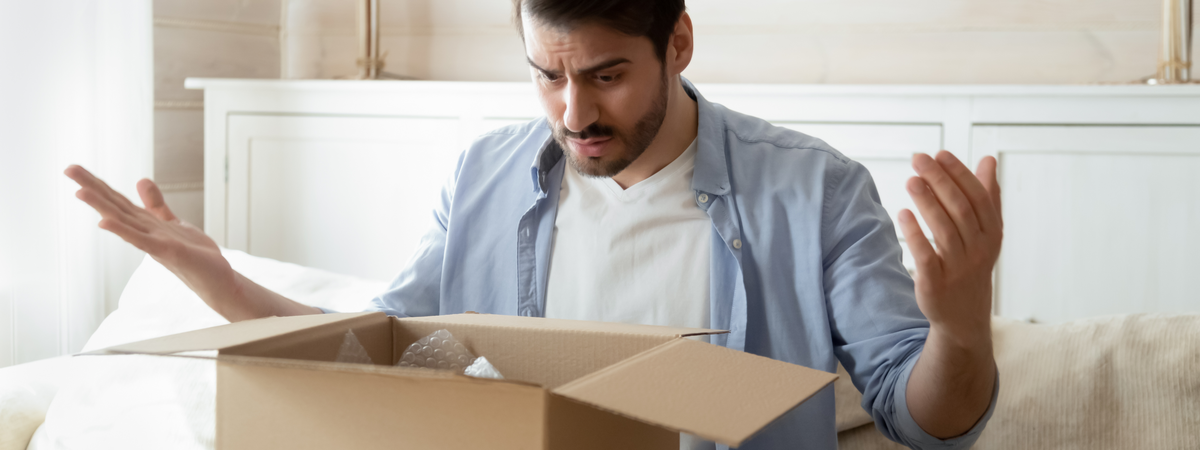
Customer Retention
Through high-quality reverse logistics, companies will improve their customer retention rates. Having an easier and better means for returns can provide pivotal points in customer and brand relationships. Ensuring the customers have a convenient and thoughtful returns process will increase the likelihood that the customer returns to your brand for future purchases.
How to Optimize Reverse Logistics
While reverse logistics can provide many benefits, industry professionals must know how to optimize the results of the reverse supply chain. Supply chain optimization within reverse logistics includes the following.
Automation
Automation continues to become a recognized, powerful disruptor within the supply chain as itcan solve a number of long-standing warehousing issues and avoid the hassle of understanding what is reverse logistics and its pain points. Consider how automation reduces the workload of managing any process. Thus, successfully applied, tech-driven automation in the reverse supply chain can address forecasting, labor costs, and fraudulent costs. Costs for automation can have a high price; however, the greater use of technology has the potential to significantly reduce both losses and expenses by automating the backward flow of goods.
Outsourcing
A highly efficient way to optimize reverse logistics departments lies within outsourcing the function completely to freight broker companies focused on improving shippers' customers' experience. Depending on the providers and the situation, this can be a cost-effective and quickly implemented solution. In some cases, however, this process has no room for adjustments or customization.
Optimization of Return Policies and Vendor Agreements
A crucial step in reverse logistics is to review return policies and vendor agreements to allow for optimization. Reviewing and updating vendor agreements can optimize the logistics process by creating data-backed processes that actively reduce overstock and ensure returned goods are handled properly.
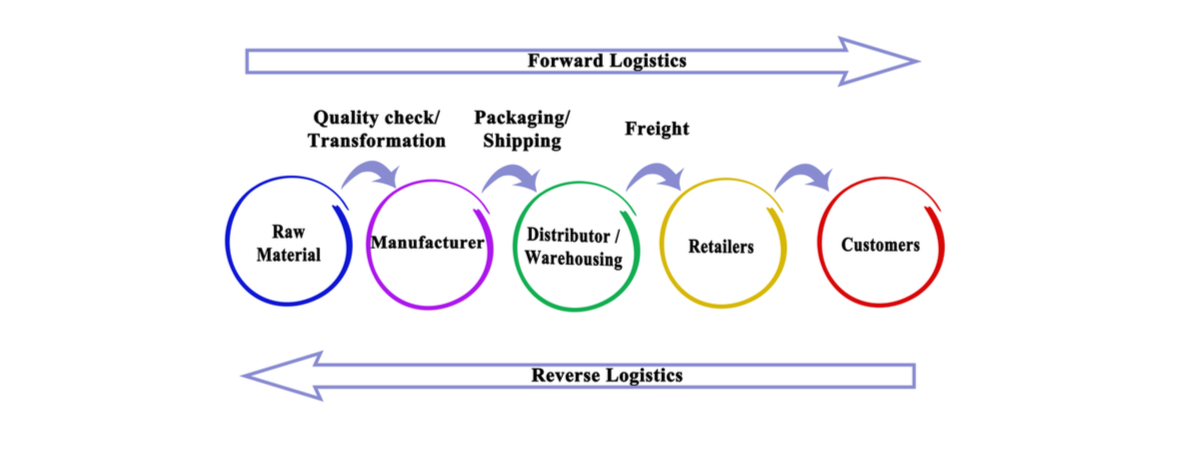
Reverse Logistics Flow vs. Traditional Logistics Flow
Traditional deals with the flow of products from the factory to the consumer or retailer, from fulfillment, and includes hub services, picking, packing, and shipping. When a certain amount of products is required, that quantity goes to a distribution center then on to retail stores. Customer demand will dictate the rate of traditional logistics, inventory will accommodate the variances in the demands. Reverse logistics is polar opposite.
Reverse logistics encompasses returns, recalls, repairs, and refurbishments of goods or equipment that may be damaged, defective, or ready for final disposal and raw material reclamation. As reverse logistics continues to expand in tandem with the growth of e-commerce, optimization is essential. Optimizing this process can provide companies with long-term benefits to build brand value while maximizing asset recovery rates and reducing costs. Additionally, reverse logistics means inventory and shipments originate at the customer or business, so it poses added challenges for managing inventory. Without a way to track those movements, such as using a returns management platform, it’s impossible to know what’s actually coming back to your facilities and in need of restocking, repair, recycling, or disposal.
Improve Your Understanding and Efficiency Within Reverse Logistics by Choosing Wicker Park Logistics
Reverse logistics efficiency yields strong benefits through cost reductions, insight into your products through data, higher customer retention rates, and more—but only if the reverse supply chain is optimized properly. To learn more about reverse logistics in your industry and to see the benefits in action, connect with the experts at Wicker Park Logistics now.